Gas turbines are critical components in modern power generation, offering high efficiency and low carbon emissions. However, the longevity and sustainable performance of these turbines is directly related to the efficiency of gas turbine air filtration systems. Mikropor offers innovative solutions that minimize maintenance costs by increasing the efficiency of gas turbines with high performance industrial filter solutions.
So which solutions are we talking about here? What are high-performance industrial filters? Which products do these filters affect the quality of and which machines are they an indispensable part of?
We have prepared a series of articles for the esteemed readers of Mikropor Library to find answers to such questions
Before diving into the details of this filter group, which has an important place in our product range, let’s first talk about what gas turbines are and how they work.
How Does a Gas Turbine Work?
A gas turbine is a continuously operating internal combustion engine. The main components common to all gas turbines are:
-A gas turbine compressor located at the inlet,
-A combustion chamber,
-A turbine on the same shaft as the compressor at the outlet.
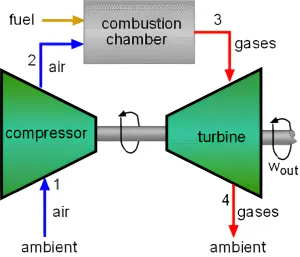
The gas turbine works with a Brayton cycle that uses air as the medium. Air at atmospheric conditions is pressurized by passing through bladed disks that act as compressors. The high-pressure air is mixed with fuel (natural gas, fuel oil, naphtha, etc.) and ignited, creating a high-temperature flow. This high-temperature compressed air enters the turbine, rotating the bladed disks and generating shaft work, which also rotates the gas turbine compressor
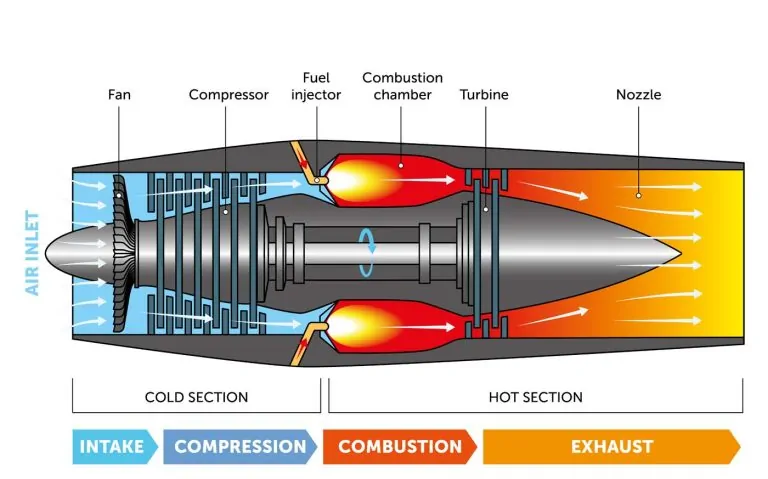
What are the Types of Gas Turbines?
Gas turbines vary according to their design and usage areas and are preferred in many different industrial and commercial fields.
Industrial Gas Turbines
Heavy Duty Turbines (Heavy Duty): High power, efficient and long-life turbines used in power plants.
Aeroderivative Turbines: are lightweight and compact turbines derived from aerospace technology. Thanks to their fast start-up and high flexibility, they adapt to harsh conditions and meet peak load demands.
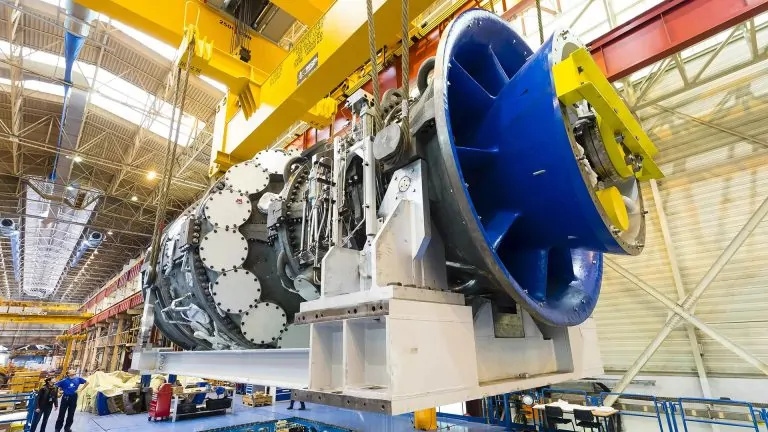
Aviation Gas Turbines
Turbojet engines: are used in airplanes to provide thrust. The gas flow from the air intake produces thrust.
Turbofan Engines: are an improved form of turbojets. More air flow is added to the process thanks to an additional fan, allowing these turbines to run more quietly and efficiently in terms of fuel consumption.
Turboprop Engines: Used for high efficiency at low speed. This variation converts the energy obtained from the gas turbine into propulsion power through the propeller.
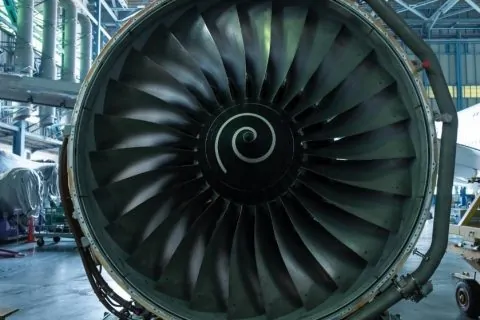
Where are Gas Turbines Used?
Electricity Generation: Gas turbines are used to generate electricity, especially in combined cycle power plants. These plants combine gas and steam turbines to convert waste heat into electricity, and are also known as cogeneration power plants.
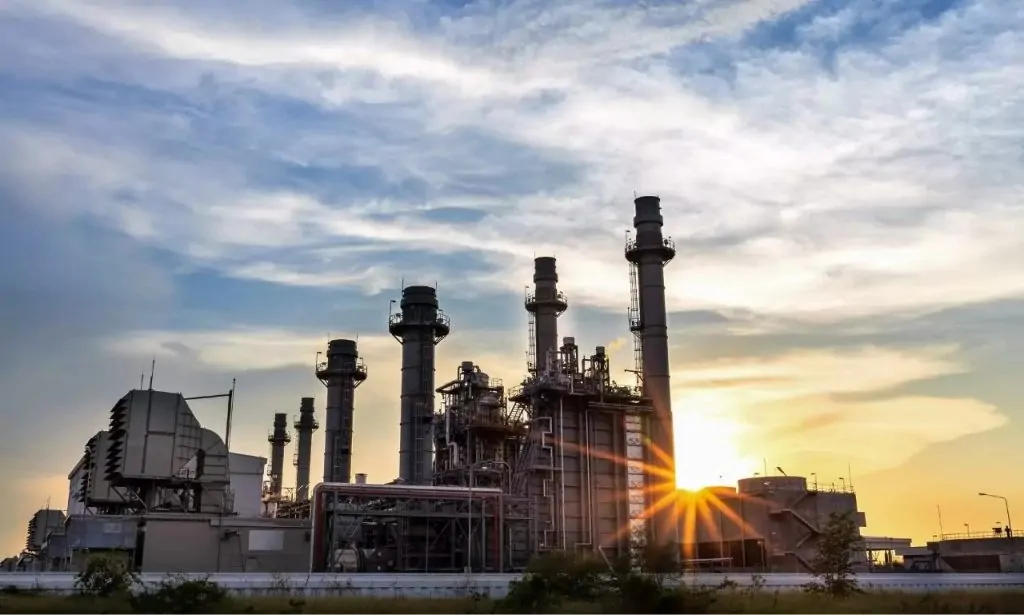
Aviation Industry: Gas turbines are the basis of modern jet engines, providing high speed and thrust in commercial and military aircraft.
Oil and Gas Industry: Here, gas turbines provide safe power to remote offshore platforms and refineries, withstanding severe weather and harsh environmental conditions in the process.
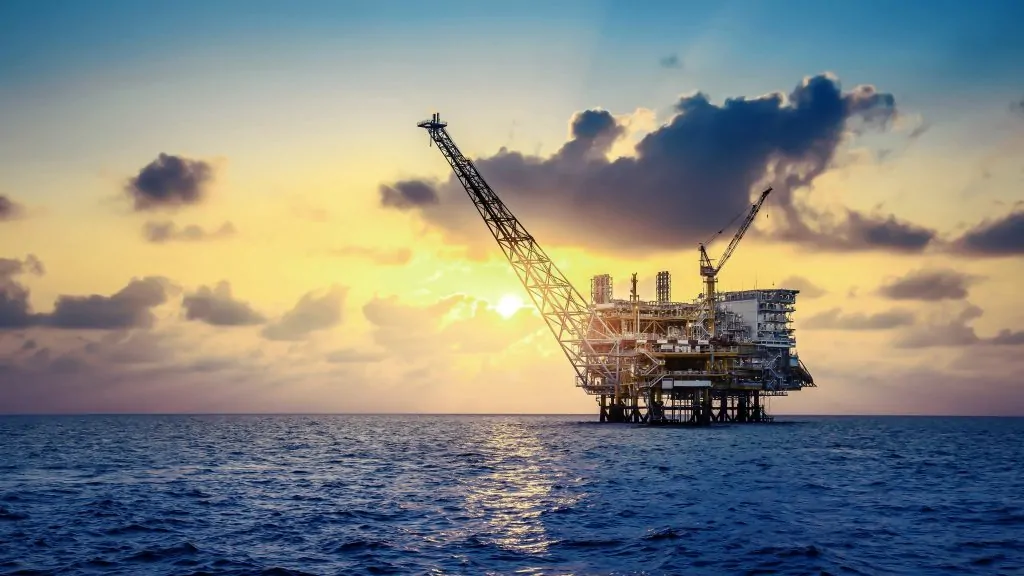
Naval: Gas turbines are commonly used in military ships. They are preferred due to their high power density and fast response times.
Processing Industries: Gas turbines are used to generate heat and electricity in the paper, food and chemical industries.
Distributed Energy Systems: Small-scale gas turbines generate energy close to consumption points, reducing transmission losses and increasing local energy security.
After talking about gas turbines and their areas of use, I would like to give a few details about their working principles.
Gas turbines have an important place in the energy sector with their various uses and benefits. However, these machines are very complex structures. Gas turbines have moving and stationary disks consisting of blades on the compression (compression, suction) and turbine (exhaust) sides. The disks on the suction side compress and pressurize the air with the drive they receive from the shaft and direct it into the combustion chamber.
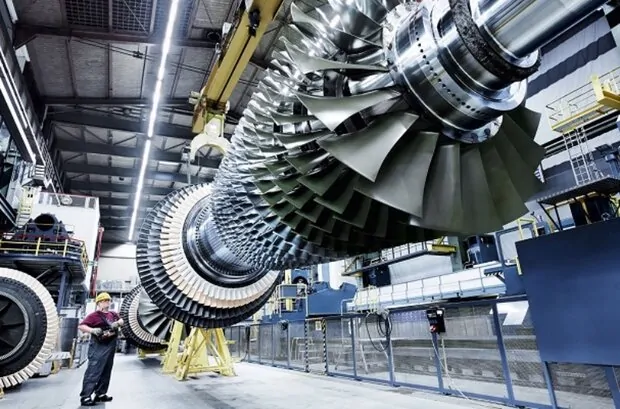
This zone is divided into two areas, low and high pressure. The average rotational speed of the disks in the LP, low pressure zone is 4000 RPM per minute. The average rotation speed of the disks in the HP, high pressure zone is up to 10,000 RPM. To withstand this rotational speed and temperatures of up to 1300 degrees Co after combustion, these gas turbine blades are coated with zirconium and ceramic. In addition, an additional cooling air sucked from the external environment is blown through holes on the blades, creating an additional barrier on the blade.
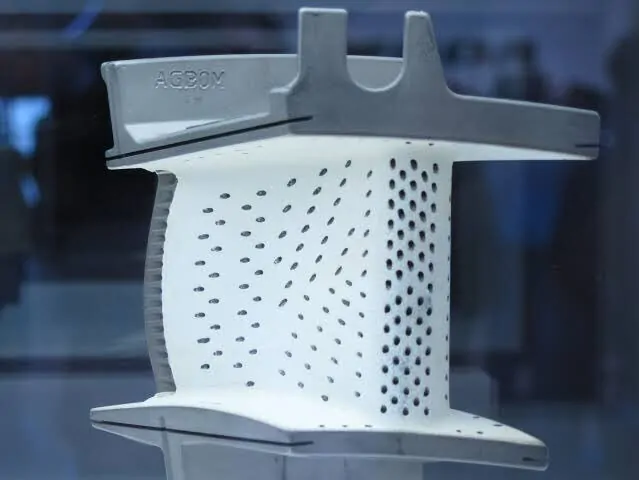
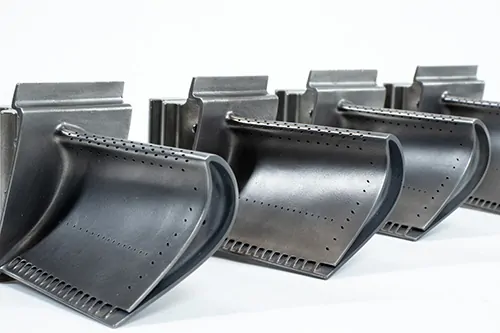
The most important and fragile point of gas turbines is this blade structure. Long-term trouble-free operation of these blades, and therefore gas turbine efficiency and gas turbine maintenance costs, depend on the cleanliness of the air sucked into the turbine. This is where the importance of air filters comes into play.
After this quick review of gas turbines and their areas of use, let’s dive into the details of gas turbine-powered power plants and their air intake systems where the filters we want to highlight are used.
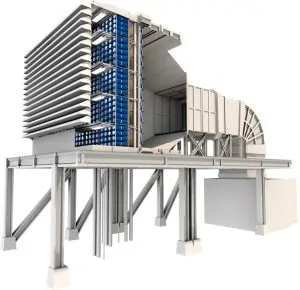
One of the most important structures that converts potential energy into kinetic energy in gas turbines is the air intake system. This system includes filter stages, self-cleaning cleaning system, evaporative cooling and anti-icing systems. According to the GT model, they filter air flow rates over 1 million m³/h at the lowest pressure loss and noise level and direct them to the turbine.
This system is generally offered in one of two configurations:
Pulse, Self-Cleaning Air Extraction Systems:
–This type contains a filter cleaning system which removes coarse particles from the filter at certain time intervals.
-Cylindrical and conical filter models are used (Mikropor MTF Series Gas Turbine Filters)
-Operating with 2-3 bar air pressure, the system vibrates the filters from the inside out and removes coarse dust of 50 microns and above.
-Filters can be placed vertically or horizontally. While vertical placement is generally preferred, horizontal placement provides better performance in environments such as deserts.
Static Air Extraction Systems:
–This type offers a wide range of uses, except in desert and polar regions.
-Multiple filter stages and different combinations can be used.
-Preferred in industrial, urban, coastal and tropical environments.
-Flexible systems that adapt to changing environmental conditions and work regimes.
-Multiple stages facilitate water use at low pressure drops and reduce the risk of bypass.
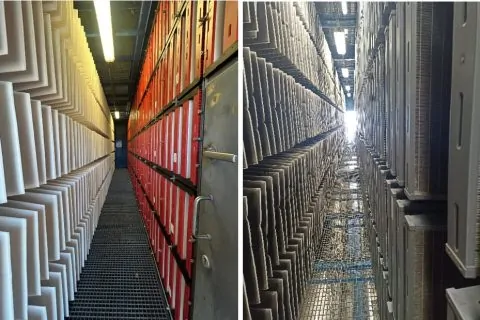
Why Jet Turbines Used in Airplanes Do Not Use Filters but Filters are Used in Gas Turbine Air Intake Systems?
The air around us contains solid particles, salt, other aggressive pollutants and aerosols that can cause clogging, contamination, performance degradation, and high operating costs. This is especially true in industrial areas where gas turbines are located.
In airplanes, the effect of altitude and gravity on airborne particles is important. Particles also have a weight and are gravitationally concentrated in the lower layers of the atmosphere. Aircraft turbines spend most of their operating time in the stratosphere layer of the atmosphere, which is 30-40 thousand feet (10-12 km) above the ground surface. The particle level in this layer is very low compared to levels closer to the surface of the earth.
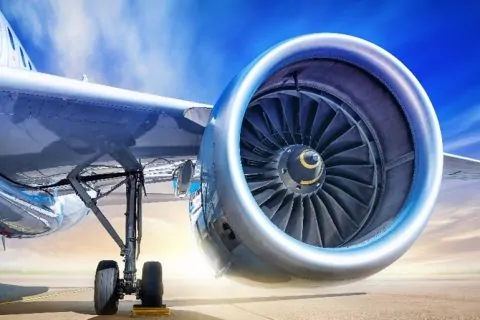
Clean air is vital for all combustion processes. But ambient air contains many particles from a wide variety of sources, from industrial processes to vegetation and transportation. The most efficient way to keep a land-based gas turbine clean is to prevent these particles from entering the turbine. Filter stages protect turbines from particles that could cause erosion, fouling or corrosion if they enter the compressor.
Particle Amount Pieces/m³ |
|||||
0.3 mic |
0.5 mic |
1 mic |
3 mic |
5 mic |
10 mic |
≥ 250.000 |
≥ 25.000 |
≥ 10.000 |
≥ 1.500 |
≥ 250 |
≥ 1 |
The table above shows the average amount of particles between 0.3 microns and 10 microns in size found in every 1 m³ of air in industrial zones. An average sized gas turbine draws in 1 million m³ of ambient air in 1 hour and forces it into the combustion chamber. This can be up to 2 million m³ in a high-end gas turbine. To give an example for better understanding, a flow rate of this magnitude is equivalent to the amount of air consumed by 10,000 internal combustion automobile engines at the same time.
In the table below you can find efficiency curves showing how efficiently different filter stages can filter particles of different sizes.
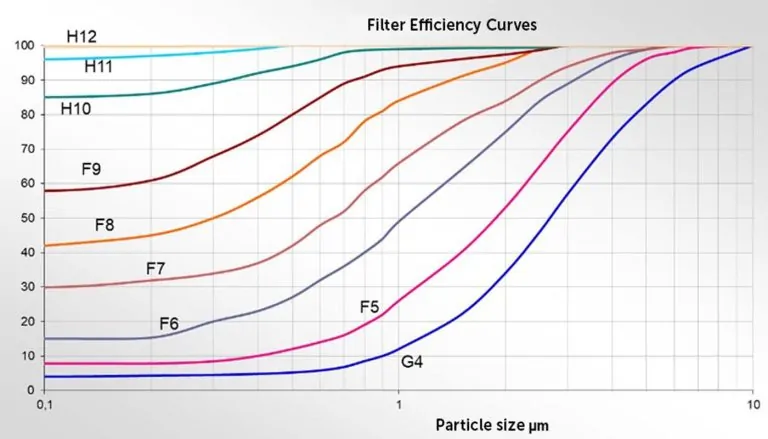
As can be seen from the efficiency table, filters of different construction have different particle efficiencies. We classify filters according to the relevant test standards EN779 / ISO 16890 and EN1822 / ISO 29463. Due to factors such as high suction power, sensitive working structure and the need for high efficiency in gas turbines, filtration stages are determined according to the nature of the working environment and are categorized as suitable for desert, seaside, offshore, tropical and polar regions.
Pulse-dynamic filter systems and appropriate filter types (Mikropor MTF) are preferred in environments with low relative humidity such as deserts, while static, multi-stage filter systems and appropriate filters are preferred in environments with relative humidity around 90% such as tropical, sea/lake shores. Coarse particles are retained by low efficiency panel (Mikropor MSKN, MSKPN-HP) and bag (Mikropor MPS, MPR) type filters, while smaller fine particles are retained by bag (Mikropor MPR) and V type (Mikropor MV, MVX) filters.
The main objective is to protect the sensitive turbine blades, prolong their life and increase the efficiency of the gas turbine. As turbine technology has advanced and new generation gas turbines (Siemens SGT5-8000 / 9000 Series, GE Frame 7HA / 9HA Series) with an overall efficiency of over 60% have been introduced, it has become necessary to use Mikropor HEPA Series very high efficiency filters as the last stage. Our Mikropor MTF, MVX and MVZ model HEPA class gas turbine air intake filters are in service on every continent in the world where such high efficiency gas turbines are found. These filters protect the turbine blades throughout the life of the filter, with the ability to retain 100% of particles 1 micron and below. Thus, turbine efficiency and the amount of energy produced remain high, while the amount of fuel consumed is optimized.
You can review Mikropor filters that offer high efficiency for gas turbine power plants here and contact our expert sales teams here.
Mikropor Sales